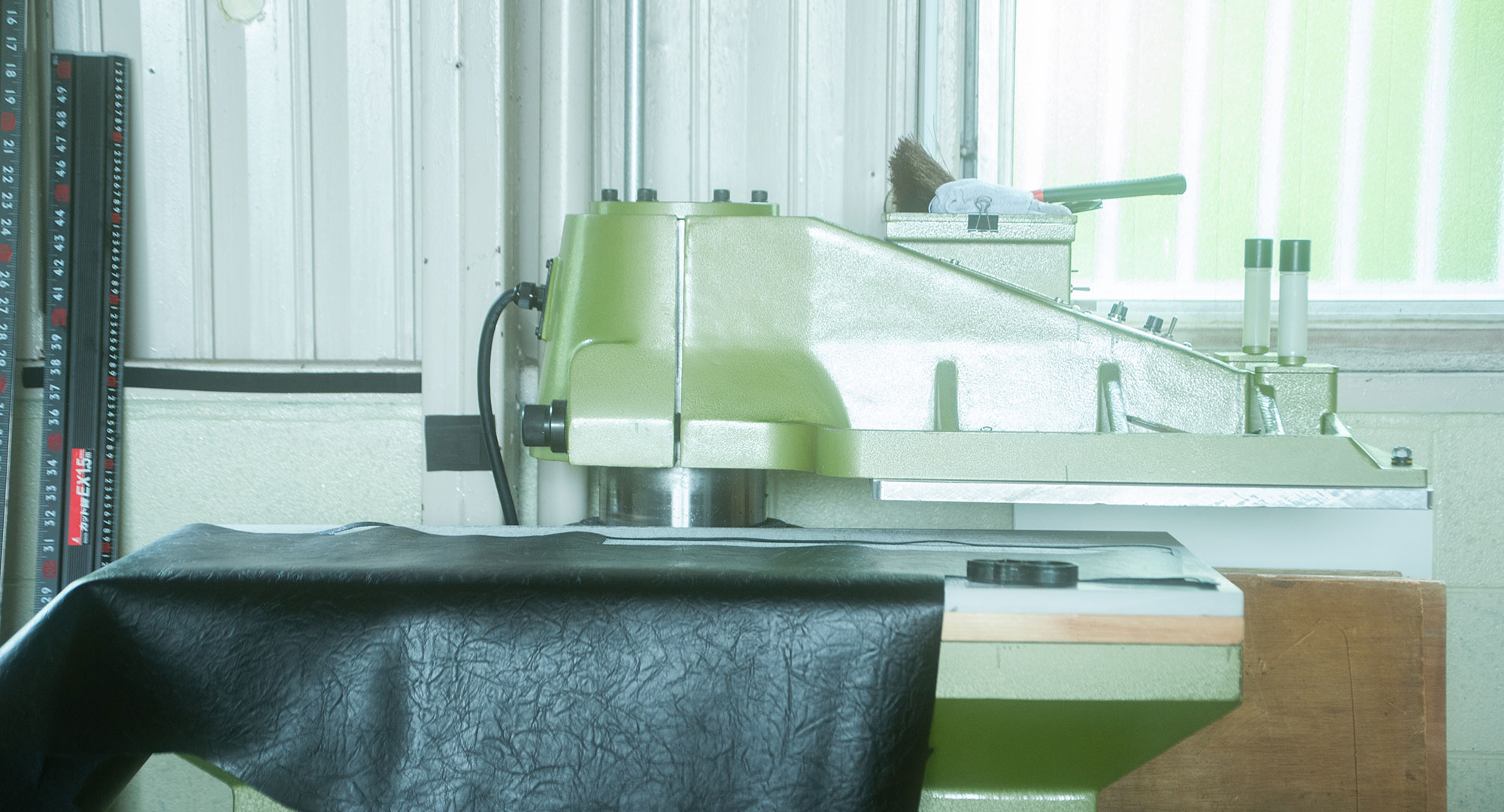
【1】企画会議、試作
新製品開発の企画会議では、デザインを練り上げながら材料を選定し、型紙サンプルを作成。その型紙を元に、試作品を作ります。
試作品をベースに、素材の色や質感などをイメージに近づけていきます。試作を何度か繰り返し、最終的な仕様を決定します。
OEM製品であれば、クライアントの要望に添えるよう試作を重ねます。より良い製品に仕上げるため、こちらから提案をさせていただく場合もあります。
お話をいただいてから仕様が確定するまで、2週間ほどかかります。
【2】素材の発注
正式に生産が決定したら、生産量分の素材を発注します。
革や布のほか、ファスナー、金具、芯材などのパーツも、一括で発注します。
革は、特殊なものであれば1ヶ月〜2ヶ月ほどの仕入れ期間が必要な場合もあります。
【3】タガネ(刃物)製作
型紙に沿って、革をプレス機で型抜きするためのタガネを、刃物業者に発注します。
【4】型抜き、裁断
タガネを取り付けたプレス機で、一つひとつ革を型抜きします。
型抜き前には、革に細かな傷をがないか、目視でていねいにチェックします。
革は、部位ごとの特性を考慮に入れて使い分けます。例えば、腹回りの革は芯材を入れるパーツに適しています。首や背中部分は、強度が必要なパーツに適しています。
帆布などの布生地は、万能ナイフを使って裁断します。
極度に薄い裏地などの素材には、レーザーと超音波を活用した「CAM裁断」という特殊な技術が用いられます。高速で裁断するので、ほつれが出ないという特徴があります。
【5】革漉き
革を専用の機械で漉き、部分的に厚みを薄くする工程です。
例えば、革と革を合わせて縫うとき、革に厚みがあると重ね縫いができなくなります。そのため、縫い代の部分だけを薄く漉く必要があります。
組み合わせによっては、5重、6重の重ね合わせが必要になります。特に、コーナー部分などの縫い代部分が直線的ではない部分は、仕上がりをイメージして漉かないと、デコボコになり美しく仕上がりません。また薄過ぎると耐久性に乏しく、破れてしまいます。職人の高度な技術が求められる工程です。
【6】折り込み
漉いた縫い代部分を折り込んで、キレイに成形します。コーナー部分などは菊折りにして仕上げます。
折り込みを均一にしないと、縫い合わせたときに仕上がりがデコボコになるので注意が必要です。
【7】コバ(切断面)塗り
ほつれやすい革のコバ(切断面)に染料を塗り、補強する作業です。コバ塗りをすることでほつれの心配がなくなり、製品の寿命が長くなります。
断面を磨いてから溶剤の「ふのり」を軽く塗り、その上から染料で塗装します。ふのりは調合を工夫し、染料がはがれにくいものにしています。また染料は高品質なイタリア製を使用しています。
非常に細やかな作業で、点数も多いことから、コバ塗りだけで1週間ほどかかることもあります。
【8】貼り合わせ、縫製
パーツを貼り合わせ、ミシンで縫製します。
革を重ねる枚数や縫い上げの角度、縫い代の形など、異なる条件の縫製を一つ一つ行っていきます。ミシンの押さえを削ったり溶接したりして、作業しやすいように加工する場合もあります。
革を強く押さえると、ミシンの跡やキズが残るので、細心の注意を払います。
【9】仕上げ
縫い合わせ部分を磨いたり、ファスナーや引き手、かしめ、ボタンを取り付け、ショルダーの穴開けなどを行います。製品としての形が仕上がります。
【10】検品・出荷
製品に不備がないか目視で検品します。チェックを通過したものは、汚れやほこりを拭き取り、ワックスを掛けて完成となります。
最後に、あんこ(緩衝材)を中に詰めて出荷されます。
あんこは自社製で、テープを使わずに適度なサイズに折り曲げられるので、製品を傷つけることはありません。